The Euclid Satellite project a good example of Philtec’s sensors being used with excellent results in cryogenic conditions. A technical paper published in 2012 shows Philtec’s high precision sensors were successfully used at 150°K to verify the distortion of lens holders to be <1 micron, well within the project requirements.
This month Philtec has again delivered sensor systems for space telescope lens distortion measurements. These are 2-channel fiber optic displacement sensor systems designed for 3.2 mm operation in vacuum.
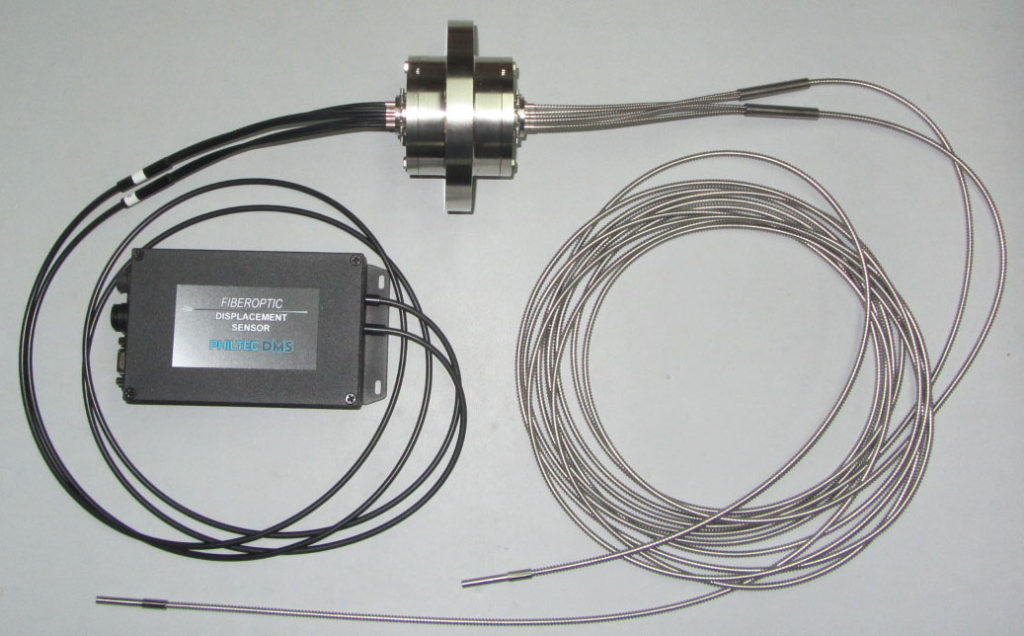
Seven 2-channel sensor systems were delivered with the following options:
- Multi-Channel Vacuum Passthru Assembly in 120 mm Custom Flange
- SS Interlok Cable Jacket in Vacuum
- 6m Total Fiberoptic Cable Length (1.5 in air, 4.5 in vacuum)
- Low CTE Invar Tips
The fiber optic cables are trifurcated for connection to the vacuum passthru (one transmit bundle and two receivers). With 14 sensor channels x 3 legs each, 42 vacuum ports were required. Each BvF120 has 16 ports, and therefore three BvF120 assemblies were used to pass all channels.
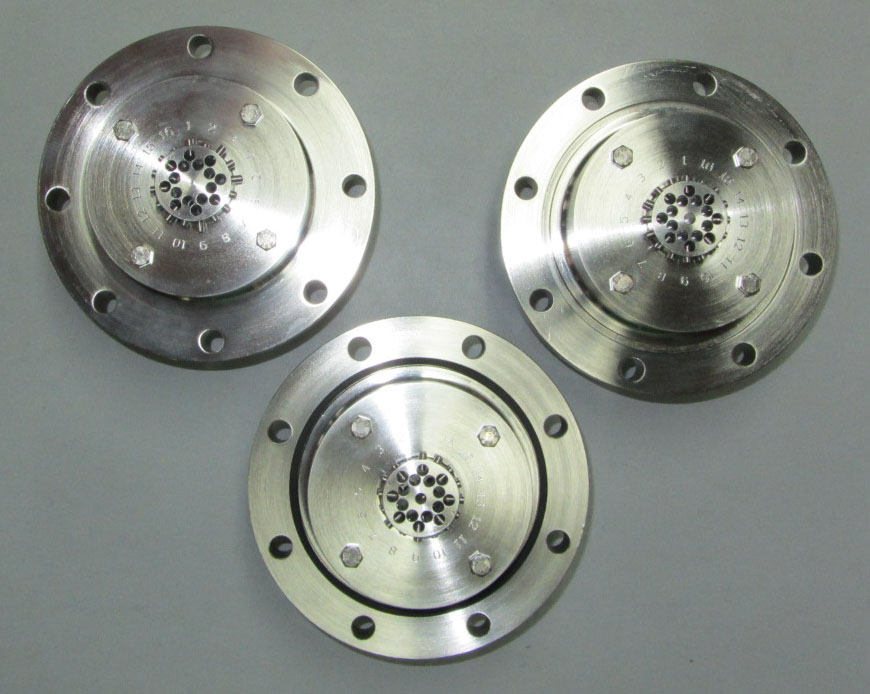
REFERENCE
‘Test Results of High-Precision Large Cryogenic Lens Holders’, 2012, Proceedings of the SPIE Publication “Modern Technologies in Space- and Ground-based Telescopes and Instrumentation II”.